Quality from the Start:
How VTEC’s Commitment to Excellence Delivers Real-World ROI in Pressure Vessel Fabrication
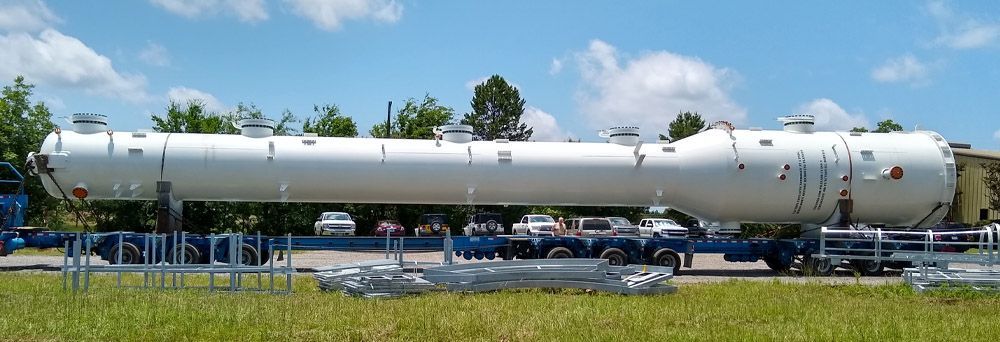
In the world of pressure vessel fabrication, quality isn’t just a matter of pride—it’s a matter of performance, safety, compliance, and cost. At
VTEC, we’ve made quality a cornerstone of our operation, embedding it into every phase of design and production. This dedication starts where it matters most:
in our Inspection Department.
Why Quality Matters in Pressure Vessel Fabrication
Pressure vessels operate under some of the harshest conditions in industrial environments—extreme temperatures, high pressures, corrosive materials, and unforgiving schedules. A single overlooked weld or a slightly misaligned nozzle can cause:
- Costly installation delays
- Unscheduled shutdowns
- Rework in the field
- Safety risks and code violations
- Potential environmental penalties
This is why every vessel that leaves VTEC’s facility is more than just “done”—it’s ready for service.
The Inspection-First Philosophy
At VTEC, we don’t see inspection as a last-minute checkpoint—we view it as a critical launch point for ensuring vessel integrity from day one. Our dedicated Quality Assurance and Inspection Department plays an active role throughout the fabrication lifecycle:
- Pre-fabrication checks to verify material certifications, design compliance, and dimensional accuracy
- In-process inspections to monitor weld quality, NDE (non-destructive examination) testing, and dimensional controls
- Final inspections with rigorous testing procedures to ensure that vessels meet or exceed ASME standards and customer specifications
This level of detail and precision ensures our customers receive “installation-ready” vessels that require minimal (if any) on-site adjustments.
Quality That Pays Off: Real ROI
Let’s talk numbers. When customers invest in a high-quality pressure vessel from VTEC, they’re not just buying steel—they’re buying performance reliability, long-term savings, and lower project risk.
Here’s how:
CATEGORY | LOW-QUALITY VESSEL | VTEC-QUAILITY VESSEL | RESULTING ROI |
---|---|---|---|
Filed Installation Time | Often requires fit-up adjustments | Typically "drop-in" ready | Save 1-3 days of labor +crane time |
Rework Frequency | High, especially for tight tolerances | Low, due to stringent inspection controls | Avoids $10K-$50K in project delay costs |
Lifecycle Service Intervals | Shorter service intervals, more risk | Longer-lasting with proven performance | Fewer shutdowns and less maintenance |
Operational Efficency | Inconsistent pressure and flow issues | Smooth, spec-verified operation | Improved throughput and plant uptime |
Lifetime Cost of Ownership | Lower upfront, higher long-term costs | Higher upfront, lower total cost | 15-25% reduction in TCO over 10 years |
Even if the initial price difference between an average and a VTEC vessel is 5–10%, the total lifecycle value overwhelmingly favors our approach. Avoiding one unexpected shutdown, rework scenario, or safety incident can easily save six figures—not to mention the value of reputation, client trust, and peace of mind.
“Built to Perform, Delivered to Serve”
Our vessels are engineered not just to meet ASME Section VIII Div. 1 and Section I code—but to exceed expectations in real-world application. The work of our inspection team makes all the difference in this process, identifying even the smallest concerns before they ever leave the shop floor.
Once fabrication is complete, every pressure vessel undergoes a final quality audit. This includes:
- Dimensional verification with precision measurement tools
- Visual inspection to identify any weld inconsistencies or potential weak points
- Final hydrostatic or pneumatic pressure testing
- Code stamping and documentation packaging
We believe attention to detail at this stage is what separates a “passable” vessel from a “VTEC-quality” vessel.
A Culture of Quality, Not Just a Department
What truly sets VTEC apart is not just our inspection process—it’s our culture. From project managers and engineers to fabricators and welders, every member of our team understands that
quality isn’t optional—it’s essential.
We work closely with our clients’ QA/QC teams and third-party inspectors to ensure that every specification is met to the letter. Our Longview, TX facility is equipped to handle high-pressure, large-diameter, specialty alloys and complex builds that many fabricators won’t touch.
Conclusion: Ready When You Are
A high-quality pressure vessel is more than just a piece of equipment—it’s a performance guarantee. When you choose VTEC, you're not just reducing risk—you're unlocking
measurable gains in uptime, cost savings, and project confidence.
So, whether you're managing a critical shutdown, constructing a new refinery unit, or upgrading an existing process system, know this: VTEC vessels are ready for service—right out of the gate.
Want to learn more?
Visit www.vesseltechnology.com or contact our sales and engineering team to explore how we can help you achieve better performance through better quality.